“Did you know? April - June 2025"
Did you know that there can be a large difference between the Glass Transition Temperature(Tg) of polymers when the sample is in the dry or the wet (with water) state? Those working with emulsion polymers encounter this difference as a natural part of their everyday experience, as water is a very strong plasticizer. While very non-polar polymers (like polystyrene) will be little affected by water, the Tg of more polar polymers (due to carbonyl, hydroxyl, and/or amine groups in the monomers) can be significantly decreased in the presence of water. The use of functional monomers such as vinyl acids also increases the effect of the water. An example of the effect of water on the polymer Tg is shown in the plot below (here we have plotted the derivative of the heat capacity (Cp) vs. temperature):
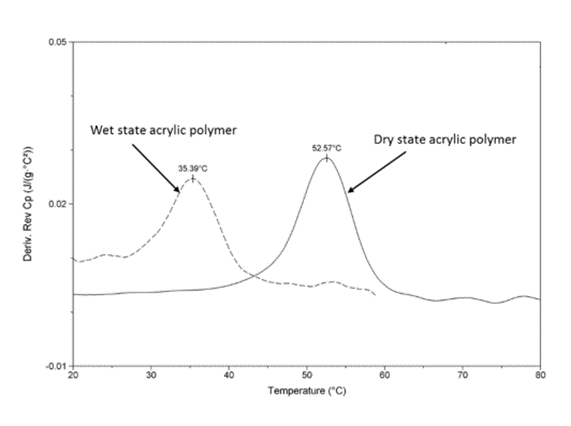
In the above data set we see a 17 °C decrease in the Tg due to the presence of water dissolved in the acrylic copolymer. Such effects are important in latex film formation, water absorption into dry films, and also in the emulsion polymerization reactions used to create the latex. This subject is treated in detail in several of our STEPn workshops, especially STEP 2 “Characterization of Latex Particles”. It is also presented in the scientific literature – Langmuir, 26, 9408-9415 (2010).
We invite your questions and comments via our website, epced.com